TK Manufacturing’s Good Vibrations
Elevating production visibility
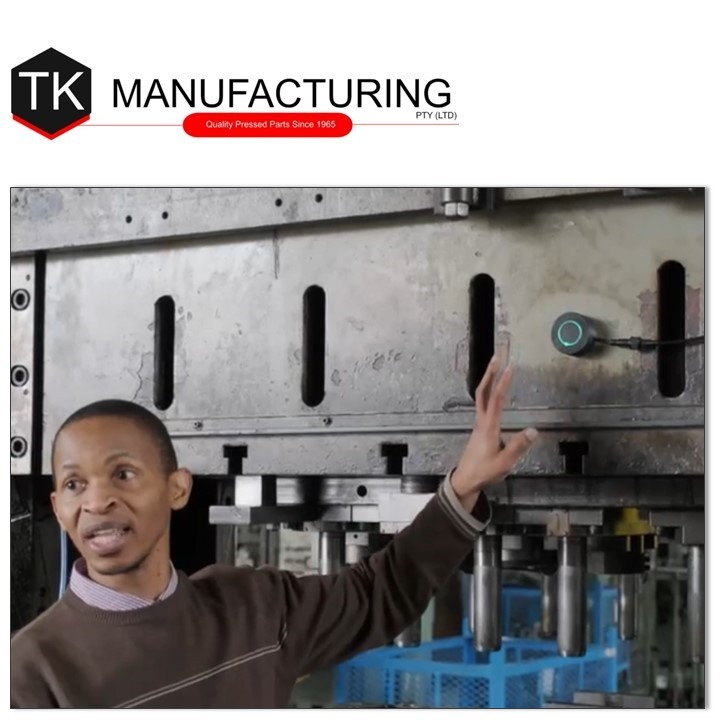
IMPACT
- Proactive insights into machine operational status
- Access to real-time production data
- Optimisation of assets
year old machine
Raven sensor
key digital insights
The Customer Journey
About The Customer
Established in 1965 by German immigrants, TK Manufacturing has firmly rooted itself in Gqeberha South Africa, serving the automotive sector with its
expertise in sheet metal forming of safety-critical parts. Operating through its two distinct divisions – TK Manufacturing for product development and mass production, and TK Toolroom Trust for tooling design and manufacturing – the company boasts an expansive workshop equipped with 30 presses and a 1 500m2 toolroom.
Adhering to ISO standards, TK Manufacturing has a global presence, supplying both direct and indirect customers with products such as brake discs, clutch plates, drive shafts, and suspension components.
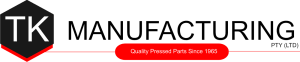
Key Challenges
However, in an era where real-time data is paramount, TK Manufacturing faced the universal challenges of outdated and disconnected machinery on some of its essential production lines.
Operational Blindness:
TK Manufacturing had limited visibility into the operational status of their machinery, leading to potential inefficiencies.
Production Uncertainty:
The absence of real-time data meant ambiguity regarding the number of parts produced at any given moment.
Asset Optimisation:
Getting the most out of their assets was challenging without precise, data-driven insights.
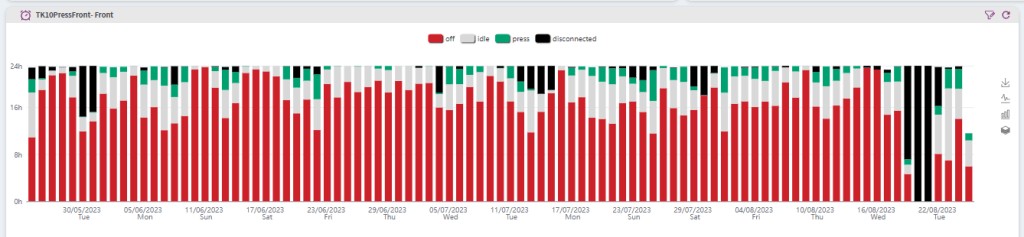
Innovative approach
Our foremost solution involved the Raven vibration sensor, an AI-powered, non-invasive tool. Remarkably, this sensor required no complex installation – it was affixed to the 50-year-old stamping press using industrial glue, connected effortlessly to a regular power socket, and integrated with the plant’s Wi-Fi.
Non-Invasive Implementation:
The Raven sensor’s non-intrusive design ensured there was no disruption to
machinery or operations. Its simple setup, using just industrial glue and standard power connectivity, demonstrates its adaptability and ease of use in diverse industrial settings.
Deep Learning Insights:
By decoding the vibration patterns of the dated stamping press, the Raven sensor delivered cycle count outputs, offering a meticulous overview of operations. This rich data was smoothly merged with the ODIN Checkpoint platform.
Universal Accessibility:
The ODIN Checkpoint app brought forth data democratisation, granting all – from the management hierarchy to the workshop floor – access to real-time production details.
Proactive Maintenance:
Beyond mere monitoring, the Raven sensor’s analysis of machine vibrations enabled a predictive approach, catalysing timely interventions to avert potential machinery issues.
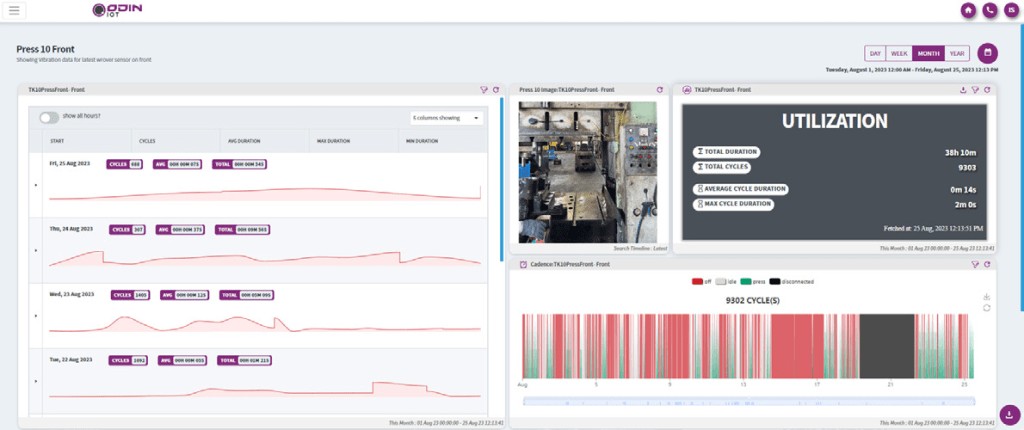
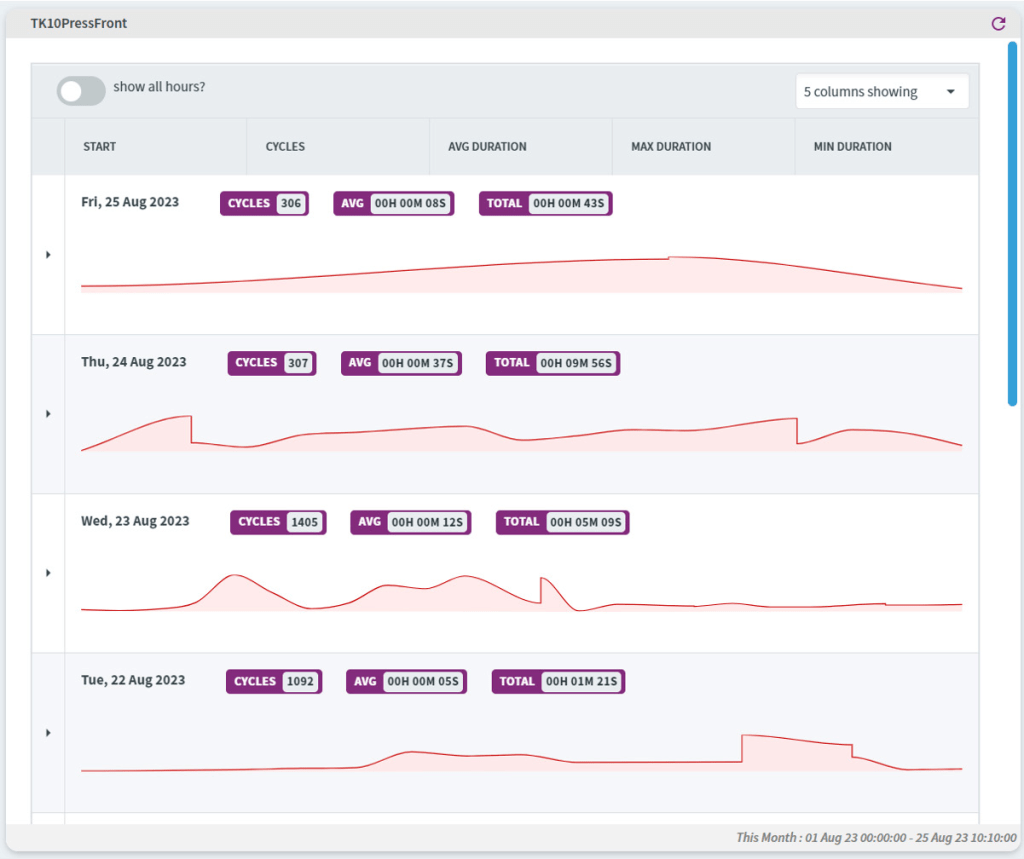
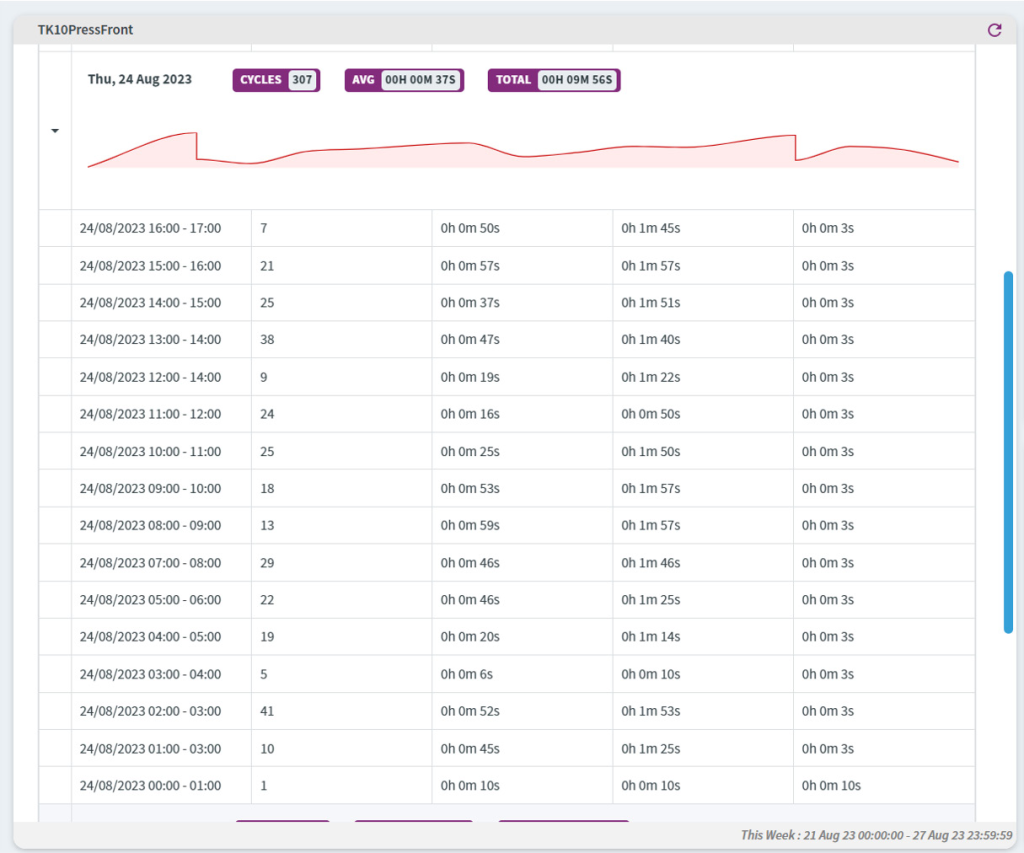
What the customer had to say
– Maynard Gesha, General Manager TK Manufacturing“Last year, four of our critical press machines went out of commission simultaneously. This incident highlighted the need for proactive machine status insights before breakdowns. ODIN Checkpoint and Raven have helped mitigate this business risk.”