CSIR’s Agile Smart Factory
PIONEERING MEDICAL DEVICE AND BATCH BUILDING
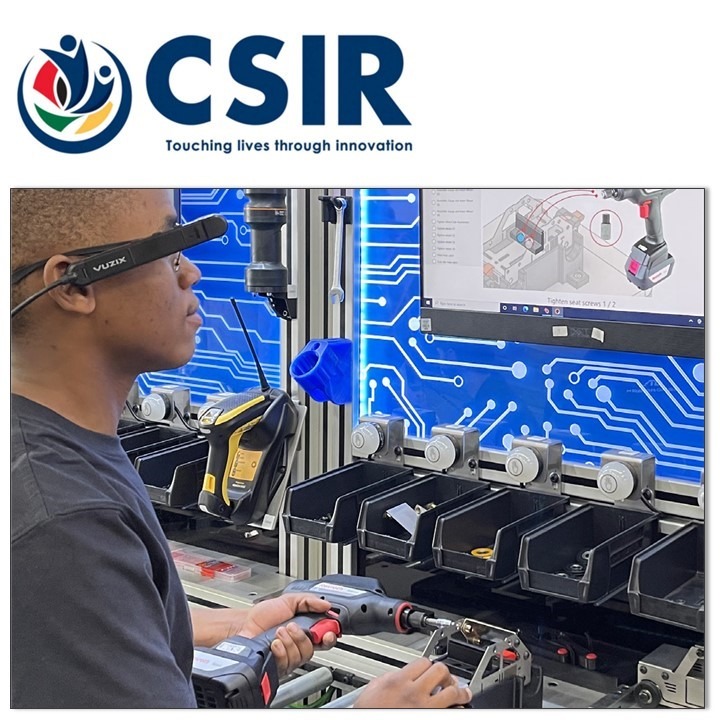
IMPACT
- Agile work cell for small-batch production
- Produce multiple models with differing components
- Short, seamless changeovers
- Strict part quality control
sec Takt time
full auto stations
manual stations
The Customer Journey
About The Customer
The Council for Scientific and Industrial Research (CSIR) in South Africa was established in 1945, making it one of the country’s oldest and most prominent research and development institutions.
With a rich history spanning decades, the CSIR has played a pivotal role in advancing scientific knowledge and technological innovation across various fields. Its primary mission is to conduct cutting-edge research that addresses critical societal challenges and fosters economic growth.
The CSIR engages in a wide spectrum of research areas, ranging from health and biotechnology to aerospace and advanced manufacturing. Through its collaborative efforts with academic institutions, government agencies, and industry partners, the CSIR contributes significantly to South Africa’s scientific progress and technological prowess, playing a vital role in shaping the nation’s future.
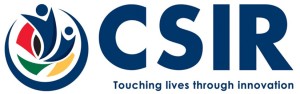
20/20
A division within CSIR was tasked with assisting small and medium manufacturers with product industrialisation. Establishing an agile factory would allow support for initial production runs, encompassing process planning, prototype builds, and first production and assembly of the customer parts.
In 2020, at the height of the Covid-19 pandemic when global demand for medical devices that assist with breathing surged, the CSIR reached out to acquire a small ODIN Workstation cell consisting of 3 stations, which was later upgraded. It was then requested that we design a larger “smart factory” that could accommodate additional parts. With hindsight being 20/20, they realised that this was the ideal means for them to create an additional revenue stream, with an agile work cell that could be updated and used for an array of different assemblies. This was an extremely cost-effective solution, as the assembly of any part is traditionally completed on its own assembly line.
The customer also required capabilities such as operator guidance to effectively manage product assemblies as well as the changeover processes to accommodate a different part. Added benefits would include process security and the ability to access part history data directly from the system after part completion.
The CSIR has successfully harnessed the power of agile manufacturing and advanced technology to create a transformative solution for small and medium manufacturers.
Work It
This new line consisted of 5 stations and 1 inspection station equipped with a Dobot, which is a small, collaborative robot that can be programmed to assist a human operator. The line was equipped with ODIN Workstation, which is what enabled access to the various part/model data and associated work instructions.
Various AI computer vision systems were integrated. Using machine learning algorithms, these systems enabled the use of “phantom devices” and also identified hand and tool positioning. These “phantom devices” emulated other physical items, as was the case with the part bins at the station. If, for example, an operator reached for a part that was incorrect in the build sequence, the system would alert to an issue and not allow the assembly to start. The same applied to the positioning of a bolting tool, which customarily, when communicating with ODIN Workstation would also yield and store torque values. It still did this, but also ensured the correct positioning of the bolting tool in relation to the part.
A flow meter was also integrated with ODIN Workstation to ensure that every part’s results are recorded, ensuring compliance and data analytics should it be required.
The stations that form part of this assembly line are standalone units and can be configured into whatever layout best suits the sets of parts being built. Each station also features removable part bin racks, so that assembly components can be placed or replaced where necessary to produce different product batches, which makes this probably one of the most agile assembly lines in the world. Each product is uniquely assembled in the work cell, with minor adjustments between different parts, such as changing out part trolleys and tooling plates. This transformation creates an ultra-flexible and agile production line, empowering the CSIR to support small and medium enterprises through the initial industrialisation process.
The Magic of Agile
In 2020, the initial parts being built included the BiPap and CPap devices, both of which are devices that assist with breathing or oxygen regulation. If the line needed to produce 100 CPap devices but also a batch of BiPap devices, the assembly run at the work cell could be completed with an almost negligible changeover.
The setup at each station is entirely generic and limited only by the customer’s imagination. The same five stations can be used immediately to build a different part because the stations share part bins for each model. A pick-to light system, which communicates with ODIN Workstation, is guided by the work instructions on what part needs to be selected at a given step. A green light will display above the part bin and the integrated camera systems are able to detect if the operator is selecting the indicated component.
Conclusion
The CSIR has successfully harnessed the power of agile manufacturing and advanced technology to create a transformative solution for small and medium manufacturers. By establishing a versatile and adaptable “smart factory”, CSIR not only addressed the challenges posed by the pandemic but also unlocked a new avenue for revenue generation.
The implementation of an ultra-flexible assembly line/work cell that integrally maintains communication between operator, part, work instructions and tooling – guided by AI and machine learning – has enabled rapid changeovers between different product batches, significantly reducing downtime and increasing efficiency.
This innovation has proven invaluable in supporting initial industrialisation processes for various products, such as the BiPap and CPap devices. CSIR’s commitment to technological innovation and collaboration underscores its vital role in shaping South Africa’s scientific progress and economic growth, marking a significant milestone in the institution’s rich history of research and development.