Audi in Aurangabad
MAXIMISING MANUAL OPERATIONS FOR COMPLEX ENGINE ASSEMBLIES
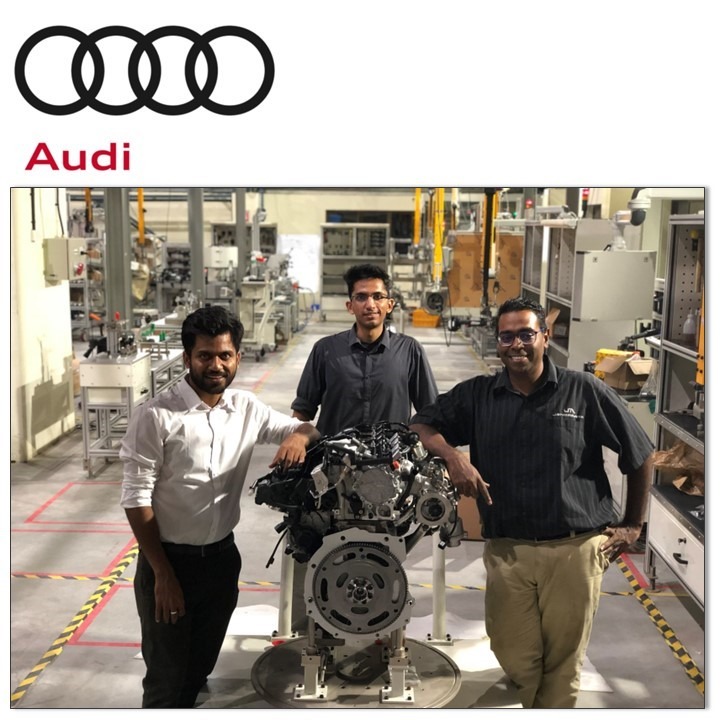
IMPACT
- Reduced training times by up to 50%
- Improved quality via higher first-time through-rates
- 200% increase in production output with reduced Takt times
stations in original
line setup
stations in reworked
line solution
operations per
station
The Customer Journey
About The Customer
Audi, the renowned German automotive brand, had their key European base of operations for engine assemblies in Gyor, Hungary, but saw the opportunity to localise engine assemblies in India at the Skoda plant in Aurangabad.
Most automotive assemblies are fairly complex, but an engine is one of the most complex. This is due to the critical components required to ensure the effective and safe operation of the engines being built.
In the Aurangabad plant, the assembly steps needed to comply with the predefined, standardised assembly sequences that had been set as the benchmark at Audi’s other locations.
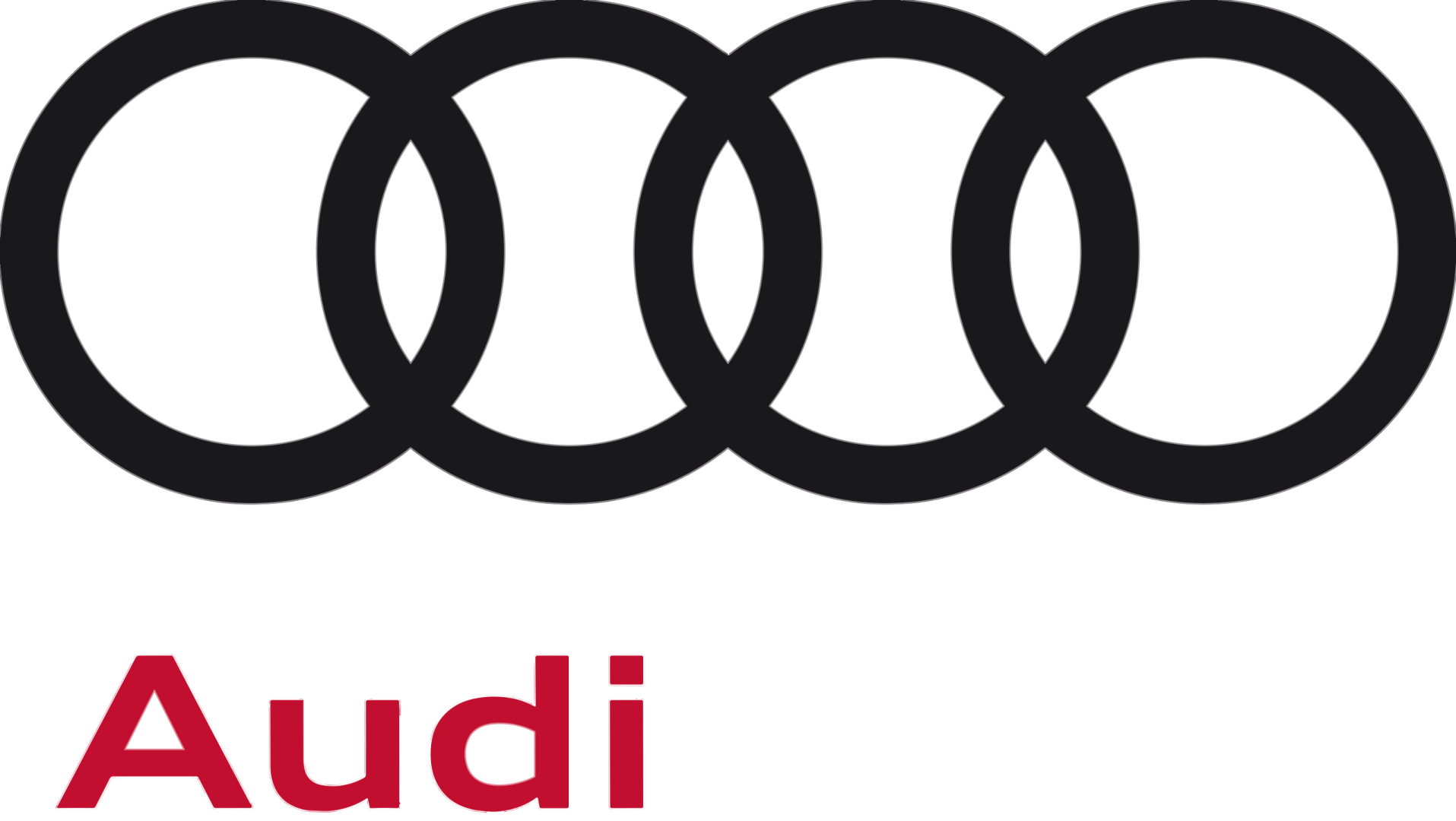
Digitisation Over Automation
Audi’s plant in Gyor stands out with its two dedicated engine assembly lines. One line serves the 4-cylinder petrol engine, featuring over 100 stations and a swift 60-second Takt time. The 6-cylinder diesel engine line has 60 stations, with a Takt time of 90 seconds. Together they produce a diverse range of 60 engine variants.
Notably, Gyor’s setup relies mainly on semi-automatic and automatic stations, catering to high-volume, high-complexity production.
For the anticipated lower production volumes in India, however, investing in such intricate and expensive assembly lines would be impractical. Instead, the vision was to create a low to no automation, yet wholly digital, assembly line. This innovative line would be tasked with producing both engine models, encompassing all 60 variants, but would compress the process into just one line with 6 stations and 6 operators, meaning that every operator would perform up to 130 operations per station.
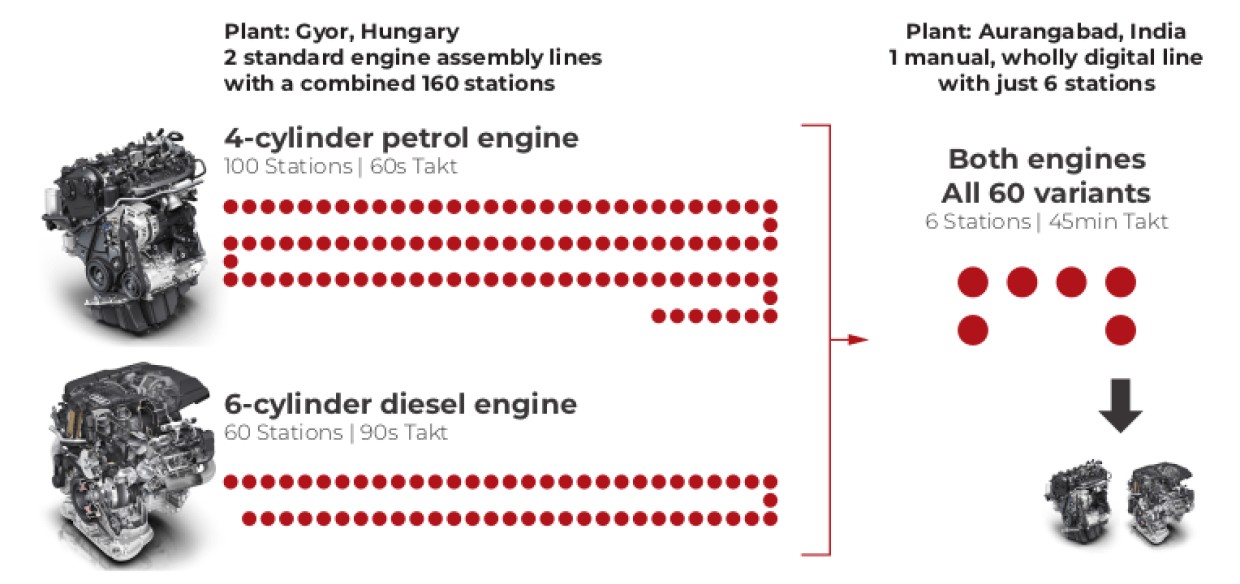
ODIN Manufacturing’s primary objective was to craft an agile, budget-friendly, manual assembly line. This setup would have to maintain the integrity of work for every model variant and adjust to shifting production demands. Operators would need to be trained while upholding production rates. Moreover, tracking parts and ensuring the highest quality assurance was paramount. Additionally, we had to address scalability and ensure smooth modifications to the assembly line.
Each component that forms part of the assembly is also tracked through unique identifiers that are either scanned or manually inputted. The work instructions, which feature both visual and text elements, aid in guiding the operators with meticulous accuracy to meet requirements.
Without this high-level worker guidance prompted by the ODIN Workstation software, it would be extremely unlikely that each operator could successfully complete up to 130 process steps. Bolting operations, for example, must be done in a specific sequence and to the correct torque.
The ODIN Workstation interface either confirms or invalidates the operation, which is a key factor in ensuring that specified quality standards are met and the integrity of the predefined assembly steps maintained. This is why the relationship between the operator, hardware and work instructions is so critical.
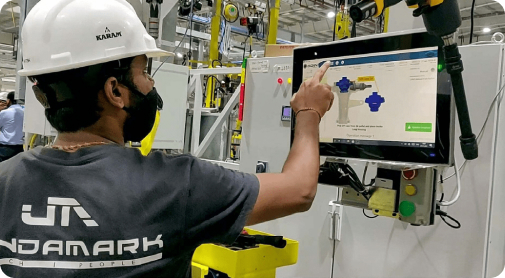
Bridging The Gap
ODIN Workstation’s no-code interface means that process engineers can update, improve and add to the existing work instructions without making changes to the software itself. It is also accessible from one point, so there is no need for process engineers to update work instructions at each station individually.
The visual step-by-step instructions help to speed up the training on a line, but on-the-job training is not the only benefit.
This platform has been shown to motivate operators, improve their understanding of the part being assembled, improve the quality of their work, bolster their confidence, all while fostering autonomy and encouraging them to put forward suggestions for process improvements.
Conclusion
Audi’s strategic decision to establish this manual assembly line marked a significant step towards achieving optimal operational efficiency and addressing the challenges that production presents in a rapidly developing manufacturing space. By opting for a more digitised approach over full automation, this project successfully demonstrated the viability of a streamlined, cost-effective, manual assembly process, factoring in various models and their respective variants, while maintaining full traceability and quality of process and part.
ODIN Workstation not only ensured error-proof assembly sequences, but also empowered the operators with its enhanced learning capabilities and skills development. This innovative approach bridged the gap between human operators and these very intricate engine assemblies. Through this partnership, Audi, with the help of ODIN Workstation, showcased the synergy between technology and human expertise in achieving excellence, setting a precedent for future advancements in the manufacturing sector.
Next Steps - It Takes Two
Two years later, Audi increased the production rate of their engine assembly line by adding a second operator to each station. This change posed challenges in coordinating bolting tool use and maintaining quality standards, but the team were ultimately successful in doubling the production rate while maintaining the expected quality standards. The line balancing at each station required careful consideration, and the synergy between the 2 operators had to match. The operators were able to work in unison and produce the same engine assemblies in half the time, enabling Audi to meet the growing demand for new vehicles in India.