Mahindra masters
multi-variant assembly
Reducing rework and scrap
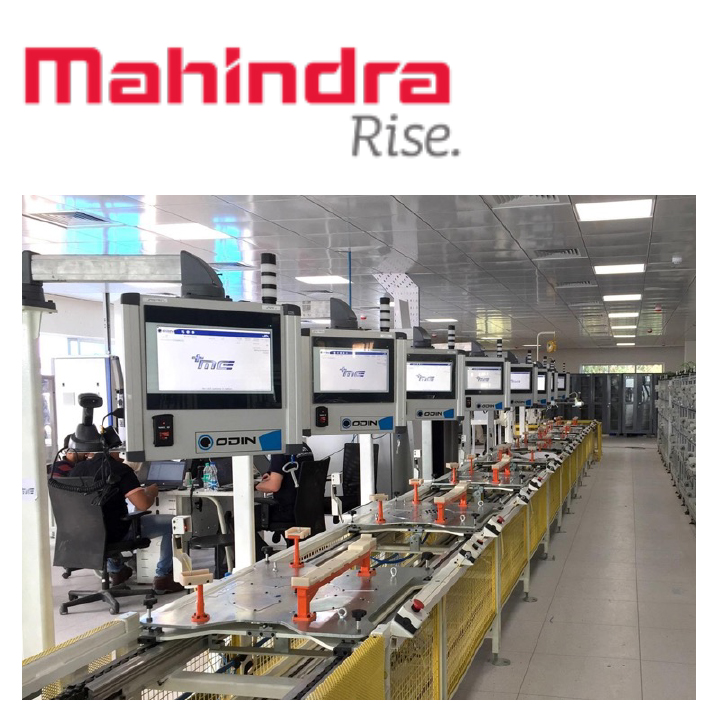
$12bn turnover, 250 000 employees, 150+ locations, in 100+ countries
By introducing digital work instructions and live production line data, Mahindra achieved a 60% cost reduction on newly introduced variants and revolutionised the way forward.
The Challenge
Ever-increasing costs associated with introducing new variants and/or models to the production line. Contributing factors included facility inefficiency, scrap and rework – with additional delays from operators who require on-the-line training.
How Did We Do This?
- By implementing ODIN Workstation throughout the line.
- By implementing ODIN Documentation to ensure one point of data access.
Benefits
- Additional failsafe measures are part of the default system features, aiding operators in ensuring that the correct parts are always used and correctly positioned.
- Live Andon displays current production targets, line progress and status above the production line, ensuring full line transparency.
Results
- Visual and dynamic work instructions provide easy integration onto the line and better understanding of product and sequences for operators.
- Fewer facility delays and improved OEE on new variant introductions.
- Reduced scrap and rework rates.