Bharat Forge’s
dynamic production
Developing a secure process sequence
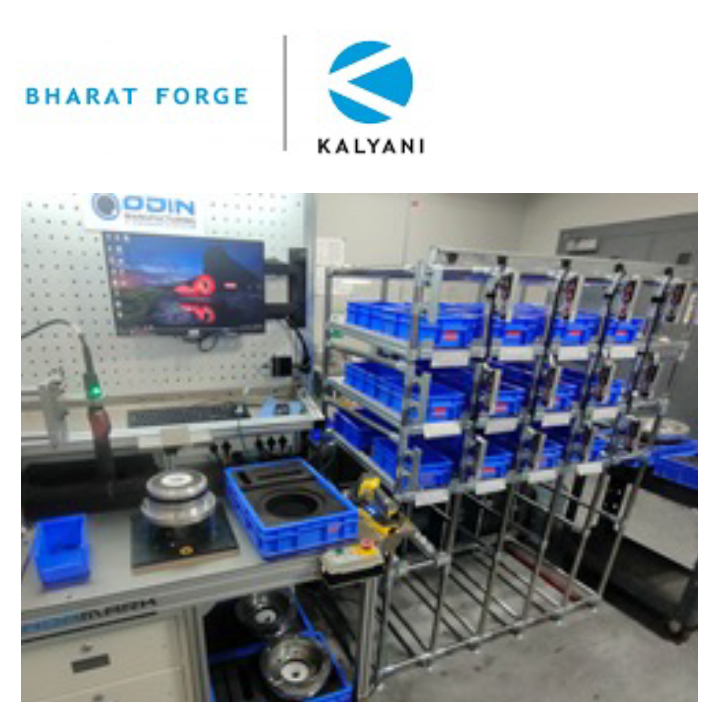
$2m turnover, 250 employees in North Carolina
Dynamic sequencing of extruders and software interlocking of child part use ensured the quality of the process was maintained.
The Challenge
Set up a systematic process flow with full process security for a dynamic production sequence.
How Did We Do This?
- By developing a process sequence and setting up ODIN Workstation accordingly.
- By developing code and logic to create interlocks for the use of child parts.
Benefits
- Operator guidance system ensured the correct assembly of the extruder.
- Multiple cameras and tightening tools were integrated with ODIN Workstation to create a fully controlled system.
Results
- Software interlocks checking part use, and interlocking based on that, ensured the quality of the assembled part.
- The traceability of part usage was digitalised and improved.