Tork’s EV excellence
Building better battery packs and motors
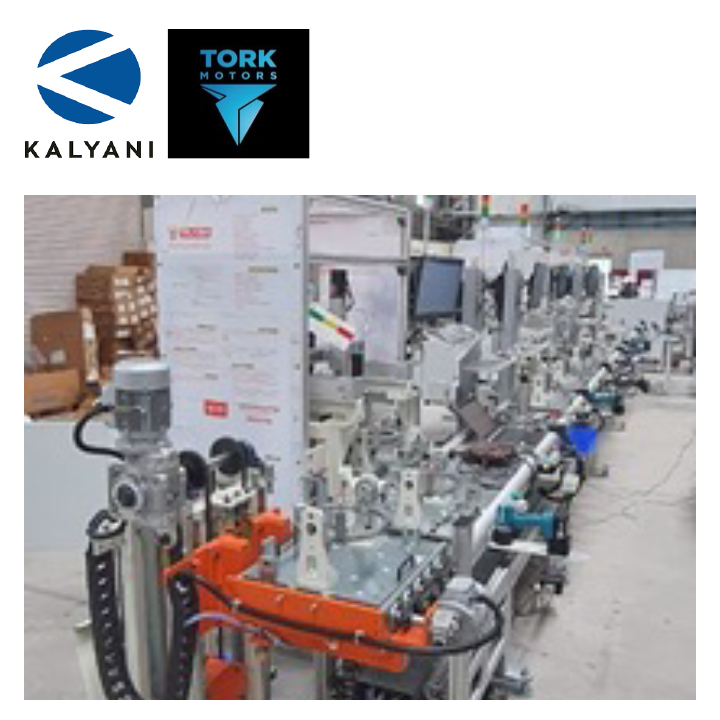
$4.5m turnover, 243 employees in Pune
Battery pack and motor assembly lines were built, with all critical operations being controlled by ODIN, ensuring 100% process security and quality output.
The Challenge
To set up electric drive train assembly lines (battery pack and motor) with battery testing and cell sorting traceability and control. The requirement was full cell level traceability under the Indian Government’s AIS156 rule.
How Did We Do This?
- By implementing ODIN Workstation throughout the entire line for each process.
- By developing code and logic to transfer specific data from specific stations and control all quality parameters like OCV/IR in building a battery pack.
Benefits
- Operator guidance was really helpful as the part was newly developed and operators were unfamiliar with the assembly process.
- Constant product developments were easily updated in the ODIN system, using a no-code interface to change process steps, sequence, operator guidance and process parameters.
Results
- Cell testing parameters of OCV/IR were recorded and cells were graded based on that.
- Motor and battery pack testing data was integrated with the system.